Sr. Product Manager Rafael Nunez explains the benefits of our new electric and engine-powered rough terrain scissor lifts. Explore the differences between these two lines and discover the advanced technology and industry-leading features that set them apart.
Learn more about what makes this line totally stacked: https://www.jlg.com/en/destination/ne...
7/30/21
7/27/21
What You Should Know About Testing Requirements for Tires
The construction equipment industry has evolved many times over in the past century. It continues to strive to provide the best solutions to help our world move ahead efficiently and safely in all aspects of construction equipment use.
A significant portion of the industry relies on a long-time mainstay that keeps vehicles moving - tires. While tires may seem to be a relatively simple component compared to other equipment technology, they play a crucial role in keeping the vehicle productive, reliable, and safe.
In recent years, tire technology has continued to evolve with new concepts in tires introduced. They look much different than what most of us think of as traditional tires and require no filling medium. Much of the discussion here will apply to any tire technology, though some points will be for specific technologies.
Tires are selected for use on vehicles based on many criteria – traction / braking, speed and load rating, ride ergonomics / vibration, ground pressure, maneuverability and packaging, wear / reliability, surface marking, and stability characteristics.
The filling medium(s) chosen to occupy internal voids or spaces within a tire and how they are applied is also an important consideration. The most prevalent choices for filling construction tires are air, foam (urethane), foam and crumb rubber mixture, and rubber. Each tire fill type can affect multiple properties of a tire’s performance which we will examine below.
Traction / Braking
Tire traction can be somewhat subjective and may vary widely for vehicles covering multiple applications and markets. Testing involves subjecting tires to and operating vehicles on differing terrains and surfaces and in a variety of environmental conditions to understand how well they grip those surfaces. The ability of the tire to expel material such as rocks and mud from the tread pattern is critical to performance. Voice of the Customer (VOC) trials are often sought as feedback for new designs. Tires also directly affect vehicle braking and therefore must be carefully considered and tested to satisfy compliance with all applicable regulations.
Speed and Load Rating
Tire manufacturers rate their tires for speed as well as load carrying ability - key to meeting the primary use of many construction use vehicles. They utilize guidelines from organizations such as the US Tire and Rim Association (TRA) and the European Tyre and Rim Technical Organisation (ETRTO). Tire ratings are based on a combination of Empty Vehicle Weight (EVW) and Gross Vehicle Weight (GVW) (empty vehicle + payload) and their respective travel speed duty cycles.
Tire ratings are based on a combination of Empty Vehicle Weight (EVW) and Gross Vehicle Weight (GVW) (empty vehicle + payload) and their respective travel speed duty cycles.
Many construction vehicle tire offerings serve a multitude of vehicle applications, making it difficult for tire suppliers to publish use guidance for every application. Tire fills can also have a significant effect on the speed and load rating of tires. As a result, bench testing and / or vehicle testing is often performed that combines expected loads, speeds, tire fills, and application profiles with construction site road hazards to assure the tire performs on the vehicle as required and expected.
Ride Ergonomics / Vibration
Tires should support and enhance the vehicle driving experience. The tire design as well as the type and amount of tire fill can affect ride ergonomics and vibration. Vehicles are tested to understand adverse frequencies, vibration, or other effects that may be transmitted into the vehicle. Measurements are often collected at sensitive components and the operator’s station to quantify the effect of the entire vehicle dynamics (including tires) on those systems.
Ground Pressure
The width and diameter of tires, the tread type of tires, the type of tire fill used, and the compliance of tires all factor into how much force will be directed onto any operating surface by the vehicle. Ground pressure is important in understanding vehicle flotation with respect to soil compaction, vehicle flotation with respect to surfaces such as mud and sand, vehicle transportation floor loading considerations, and floor loading where vehicles are operating on constructed surfaces. Ground pressure is determined generally through testing and calculation to determine what percentage of each tire surface area is supporting the vehicle load on a given terrain.
Maneuverability and Packaging
Tires must allow the vehicle to achieve vehicle design requirements dimensions in width, length, turning radius, height, and steering. Wide tires can adversely affect vehicle width, the maximum steer angle possible, as well as resistance to steering due to ground contact friction. Large diameter tires can affect vehicle overall length and height dimensions of the vehicle. Tire fill types may affect how well the vehicle can maneuver. Vehicle dimensional analyses as well as multiple performance tests are conducted to assure targets of maneuverability and packaging are met.
Wear / Reliability
Tires and their filling medium must exhibit wear and structural integrity characteristics that are in line with intended industry expectations. Vehicles with tires that consume the available working tread too quickly or become damaged too easily (chunking treads, bulges / broken belts, punctures, fill compromised, etc.) will not meet customer’s expectations. Vehicle testing is undertaken on a variety of construction surfaces, applications, and road hazards to assure the wear rate is reasonable and that the tire and it’s filling medium survives structurally to reasonable expectations.
Surface Marking
Some use applications require vehicles to not mark the surfaces on which they are operating and therefore require unique tire compounds. Special applications such as this may create unique tire testing considerations for tire and vehicle manufacturers.
Stability
Of significant importance is how well the tires and their associated fill maintain their structural shape when loaded in various configurations – ultimately affecting the stability of the vehicle. Every tire option offered on a vehicle must adequately support the vehicle to meet all applicable regulations and the published load carrying capability of the vehicle. Tire type (bias ply, radial, solid, etc.) as well as fill medium can significantly affect the sidewall and overall stiffness of a tire when subjected to a combination of vertical and transverse loading. Significant testing and simulation is performed on vehicles to assure the tire options offered can adequately support the base vehicle weight and any required payload according to industry regulations, standards, and published load diagrams.
Tires are, and will remain for the foreseeable future, an integral and important component of many construction vehicles today. Their selection and use influences multiple aspects of vehicle performance that must be confirmed through a combination of calculation, simulation, and test.
Source: https://www.jlg.com/en/direct-access/2018/04/13/what-you-should-know-about-testing-requirements-for-tires

A significant portion of the industry relies on a long-time mainstay that keeps vehicles moving - tires. While tires may seem to be a relatively simple component compared to other equipment technology, they play a crucial role in keeping the vehicle productive, reliable, and safe.
In recent years, tire technology has continued to evolve with new concepts in tires introduced. They look much different than what most of us think of as traditional tires and require no filling medium. Much of the discussion here will apply to any tire technology, though some points will be for specific technologies.
Tires are selected for use on vehicles based on many criteria – traction / braking, speed and load rating, ride ergonomics / vibration, ground pressure, maneuverability and packaging, wear / reliability, surface marking, and stability characteristics.
The filling medium(s) chosen to occupy internal voids or spaces within a tire and how they are applied is also an important consideration. The most prevalent choices for filling construction tires are air, foam (urethane), foam and crumb rubber mixture, and rubber. Each tire fill type can affect multiple properties of a tire’s performance which we will examine below.
Traction / Braking
Tire traction can be somewhat subjective and may vary widely for vehicles covering multiple applications and markets. Testing involves subjecting tires to and operating vehicles on differing terrains and surfaces and in a variety of environmental conditions to understand how well they grip those surfaces. The ability of the tire to expel material such as rocks and mud from the tread pattern is critical to performance. Voice of the Customer (VOC) trials are often sought as feedback for new designs. Tires also directly affect vehicle braking and therefore must be carefully considered and tested to satisfy compliance with all applicable regulations.
Speed and Load Rating
Tire manufacturers rate their tires for speed as well as load carrying ability - key to meeting the primary use of many construction use vehicles. They utilize guidelines from organizations such as the US Tire and Rim Association (TRA) and the European Tyre and Rim Technical Organisation (ETRTO). Tire ratings are based on a combination of Empty Vehicle Weight (EVW) and Gross Vehicle Weight (GVW) (empty vehicle + payload) and their respective travel speed duty cycles.
Tire ratings are based on a combination of Empty Vehicle Weight (EVW) and Gross Vehicle Weight (GVW) (empty vehicle + payload) and their respective travel speed duty cycles.
Many construction vehicle tire offerings serve a multitude of vehicle applications, making it difficult for tire suppliers to publish use guidance for every application. Tire fills can also have a significant effect on the speed and load rating of tires. As a result, bench testing and / or vehicle testing is often performed that combines expected loads, speeds, tire fills, and application profiles with construction site road hazards to assure the tire performs on the vehicle as required and expected.
Ride Ergonomics / Vibration
Tires should support and enhance the vehicle driving experience. The tire design as well as the type and amount of tire fill can affect ride ergonomics and vibration. Vehicles are tested to understand adverse frequencies, vibration, or other effects that may be transmitted into the vehicle. Measurements are often collected at sensitive components and the operator’s station to quantify the effect of the entire vehicle dynamics (including tires) on those systems.
Ground Pressure
The width and diameter of tires, the tread type of tires, the type of tire fill used, and the compliance of tires all factor into how much force will be directed onto any operating surface by the vehicle. Ground pressure is important in understanding vehicle flotation with respect to soil compaction, vehicle flotation with respect to surfaces such as mud and sand, vehicle transportation floor loading considerations, and floor loading where vehicles are operating on constructed surfaces. Ground pressure is determined generally through testing and calculation to determine what percentage of each tire surface area is supporting the vehicle load on a given terrain.
Maneuverability and Packaging
Tires must allow the vehicle to achieve vehicle design requirements dimensions in width, length, turning radius, height, and steering. Wide tires can adversely affect vehicle width, the maximum steer angle possible, as well as resistance to steering due to ground contact friction. Large diameter tires can affect vehicle overall length and height dimensions of the vehicle. Tire fill types may affect how well the vehicle can maneuver. Vehicle dimensional analyses as well as multiple performance tests are conducted to assure targets of maneuverability and packaging are met.
Wear / Reliability
Tires and their filling medium must exhibit wear and structural integrity characteristics that are in line with intended industry expectations. Vehicles with tires that consume the available working tread too quickly or become damaged too easily (chunking treads, bulges / broken belts, punctures, fill compromised, etc.) will not meet customer’s expectations. Vehicle testing is undertaken on a variety of construction surfaces, applications, and road hazards to assure the wear rate is reasonable and that the tire and it’s filling medium survives structurally to reasonable expectations.
Surface Marking
Some use applications require vehicles to not mark the surfaces on which they are operating and therefore require unique tire compounds. Special applications such as this may create unique tire testing considerations for tire and vehicle manufacturers.
Stability
Of significant importance is how well the tires and their associated fill maintain their structural shape when loaded in various configurations – ultimately affecting the stability of the vehicle. Every tire option offered on a vehicle must adequately support the vehicle to meet all applicable regulations and the published load carrying capability of the vehicle. Tire type (bias ply, radial, solid, etc.) as well as fill medium can significantly affect the sidewall and overall stiffness of a tire when subjected to a combination of vertical and transverse loading. Significant testing and simulation is performed on vehicles to assure the tire options offered can adequately support the base vehicle weight and any required payload according to industry regulations, standards, and published load diagrams.
Tires are, and will remain for the foreseeable future, an integral and important component of many construction vehicles today. Their selection and use influences multiple aspects of vehicle performance that must be confirmed through a combination of calculation, simulation, and test.
Source: https://www.jlg.com/en/direct-access/2018/04/13/what-you-should-know-about-testing-requirements-for-tires
7/24/21
Test Your JLG Knowledge
How well do you know JLG® machines and services? Test your knowledge in our Trivia Challenge, and you could win this month’s prize: a JLG® auto tech kit.
Follow this link to test your knowledge: https://www.jlg.com/en/ground_support/trivia-2018-april.aspx
7/20/21
Service Tips: Mobile elevating work platforms
Maintenance can drive lower total cost of ownership.
By Bill Dovey
ANSI requires extensive recordkeeping of boom lift maintenance
New ANSI standards will require changes to maintenance recordkeeping.
Keep it clean
Keep it clean. Be diligent in keeping contaminants out of engine, coolant, electrical hydraulic systems and drives.
Proper maintenance of access equipment allows owners to sell and rent a safe fleet of machines and is critical to performance and uptime. Failure to properly maintain boom, scissor and vertical lifts can disrupt a project schedule and put it over budget.
Regular service of aerial work platforms (AWPs), now referred to by the American National Standards Institute (ANSI) as mobile elevating work platforms (MEWPs), is necessary to ensure compliance, prevent workplace accidents and lower total cost of ownership. Beyond the inspection checklist, here are items to consider when inspecting and maintaining aerial lifts.
ANSI standards define inspection protocols
ANSI A92.6 outlines the frequency of preventive and annual MEWP inspection requirements. Federal law requires a frequency inspection every 90 days or 150 hours, whichever comes first. An annual inspection must be performed on a MEWP no later than 13 months from the date of the prior annual inspection. Owners should consider placing MEWPs on a planned maintenance schedule based on hours of operation and type of application.
ANSI also mandates inspections be performed by a technician qualified on the specific make and model of the MEWP or one having similar design characteristics. What’s required for inspections is determined by the original equipment manufacturer (OEM). Owners of mixed fleets must reference the manual of each manufacturer for the specific piece of equipment being inspected to ensure compliance and operator safety.
Cleanliness extends service life
Dirt and foreign materials that collect on a MEWP can shorten its service life and impact resale value. Although manufacturers provide safeguards such as shields, covers, seals and filters to keep air, fuel, oil and grease supplies clean, regular maintenance is still necessary.
Openings in air, fuel or oil lines that are disconnected during maintenance should be covered to prevent dirt or other foreign materials from entering. When replacing old or damaged parts, such as oil and air filters, keep the new parts in their containers to maintain cleanliness and avoid scratching or scoring.
Prevent hydraulic system contamination
Hydraulic system fluid cleanliness is key to a long life for the system and its components. Even a small amount of dirt or other contaminant can compromise the hydraulic system. Contamination can be caused by using inadequate hydraulic oil or allowing moisture, grease, filings, sealing components or sand to enter while performing maintenance. Insufficient warm-up or leaks in suction lines can cavitate pumps and cause contamination. A tainted system can damage close-fitting parts like valves, pumps and motors, leading to malfunctions that could result in faulty operation and shorter service life.
To assess hydraulic oil cleanliness, remove filters and look for cloudy oil or metal particles. If the hydraulic system has been contaminated, it must be drained, flushed and refilled with clean hydraulic oil. The MEWP’s service manual will share how often filters should be checked, cleaned and replaced. Filters may need to be inspected more often if the machine is operating in a harsh environment.
Extending powertrain life
Many diesel engines require using diesel exhaust fluid (DEF). If the wrong fluid is added, such as screen washer or diesel fuel, the injection, ejection fluid quality sensing systems may be damaged, impacting system life.
While battery packs are unlikely to become contaminated with foreign material, they may be subject to corrosion. To clean the battery, use a non-metallic brush and a solution of baking soda and water, then rinse with clean water and thoroughly dry it. Coat the terminals with an anti-corrosion compound.
New ANSI standards compliance
ANSI A92 updates are expected to be published in May 2018 and rental companies, dealers and distributors must be in compliance within one year of its publication date.
Rental companies will be required to train technicians on the current standards for each class of equipment they service. Equipment dealers and rental companies should also help operators understand and plan for these changes. End users may face challenges with new equipment and will have questions about site training and compliance.
The new standard requires annual machine inspections (AMI); completion and expiration dates must be noted on the MEWP. If rental firms use a third party for machine inspections and maintenance beyond daily walk-arounds, they must verify that person follows the new standard.
Under the new standard, operators with suitable experience may complete self-familiarization to reduce service calls to owners for minor operational adjustments. The requirement still exists to offer familiarization, but will be on an as-requested basis. In response to this change, rental companies may choose to use alternative customer service practices.
Another way rental companies can be more efficient is by stocking commonly used parts, attachments and supplies, eliminating rush orders and saving time and money.
Several changes to the manufacturing standards of MEWPs are anticipated, including load- and tilt-sensing, wind-force requirements, entrance gates, platform railings, tires and machine markings. Many OEMs have already undertaken these functional changes; operation manuals will include these updates.
New machinery components must be supplied by the OEM and meet the OEM specs to remain compliant. For example, replacing a gate with a chain on a new machine is an unauthorized product modification and will render the machine non-compliant.
Rental companies may see an increase in requests for information on retrofit accessories and must explain the manufacturer’s new warnings and instructions to renters. Rental companies should assist end users in meeting these new obligations. Equipment owners and dealers will need to consider how to familiarize their technicians with the new features brought on by the design requirements.
Regular MEWP inspections, preventive maintenance and ongoing training will improve operator and worker safety and increase uptime of equipment fleets. Partner with OEMs to understand best practices and develop a plan for optimal fleet utilization, which will help lower total cost of ownership.
Bill Dovey is senior product manager at JLG Industries Inc.
This article originally appeared in the May-June 2018 issue of Pro Contractor Rentals magazine, © 2018 Direct Business Media
7/18/21
Experience the Worksite of the Future
In this video recap, we venture into the worksite of the future using augmented reality. Learn how advances in communication, machine design and connected technology will propel the construction industry forward.
http://www.jlg.com/
7/15/21
Product Introduction: Genie® S® 80 J Telescopic Boom Lift - ANSI
The Genie S-80 J model has an unrestricted platform capacity of 660 lb (300 kg) to get the job done with two occupants, plus tools, and a 6-ft (1.8 m) jib, leading length and capacity for low-weight booms in this height category. Learn more: https://www.genielift.com/en/aerial-l...
7/12/21
Tutorial: JLG 3-D Hydraulics Schematics Troubleshooting
At JLG, we strive to provide you with tools to make your jobs faster and easier. Machine service technicians - this one is for you! Now you can quickly and easily locate and trace a hydraulic circuit to it's function with 3-D Hydraulic Schematics. These interactive, environmentally friendly schematics are available to anyone with access to Online Express and allow you to view 3-D renderings of boom, scissor and telehandler machines to help troubleshoot any hydraulic issues. The best part? You can order the products you need right from the schematic.
7/08/21
Genie® Lift Pro™ Training | Rescue Plans
Every organization that operates MEWPs needs to develop a safe use plan and having documented rescue plans is a requirement. Learn more about rescue plans in this article from Genie® Director of Training Scott Owyen: https://www.genielift.com/en/aerialpr... #ANSI #Safety #GenieTogether
7/05/21
Similar, Not the Same
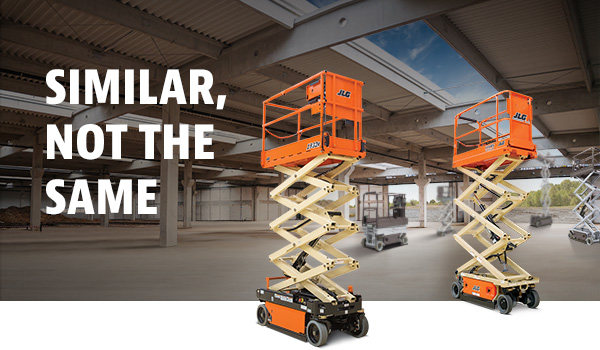
You can settle for a scissor that does the job. Or you can choose from two JLG® scissor lines that do what other brands can’t. Consider our full range of machines—from the value R to the premium ES—and get the performance you expect with smart, simple technology that maximizes your uptime.
Learn more: https://www.jlg.com/en/destination/similar-not-same
7/03/21
Find Qualified Trainers Nationwide with AccessReady from JLG
With proper telehandler training and aerial lift training, you can walk onto the job site knowing you have the right credentials. AccessReady connects operators with JLG-qualified trainers to complete OSHA and ANSI compliant training.
Learn more at: https://www.jlg.com/en/training/operator-training
Subscribe to:
Posts (Atom)